Foreword
The main component of the radiotherapy system is the medical electron linear accelerator, which is a large-scale medical device that uses microwave electric fields to accelerate electrons to generate high-energy rays, and is used for long-distance external radiation therapy activities in human medical practice. It is widely used in various The treatment of various tumors, especially the treatment of deep tumors. Medical electron linear accelerators can produce X-radiation and/or electron radiation beams. High-energy X-rays have the characteristics of high penetration, low skin dose, and high ray uniformity, and are suitable for treating deep tumors. Electron beams have certain range characteristics and low penetration ability, and are used to treat superficial tumors. The medical treatment bed is the carrier of the patient's radiotherapy. During the radiotherapy process, the impact of the bed board on the absorption of radiation dose should be considered. Therefore, the current high-end treatment bed board no longer uses aluminum alloy materials, so as to improve the bed board's transmittance to X-rays and reduce attenuation.
Application
Recently, when a hospital installed the Elekta radiotherapy system, it was found that one of the pair of connecting parts of the carbon fiber treatment bed iBeam evo expansion board was lost during transportation. The original connector is processed by carbon fiber CNC milling process. The cost of processing this part with the same material is expected to exceed 2,000 yuan, and the processing cycle is longer due to the epidemic. Without this connector, the bed support cannot be achieved. The function of the head, the progress of equipment commissioning and putting into use are expected to be delayed for more than 2 months. On the other hand, although the aluminum alloy CNC processing cycle is short and the cost is low, it will affect the X-ray transmittance of the treatment bed, and then affect the use of the whole set of equipment.
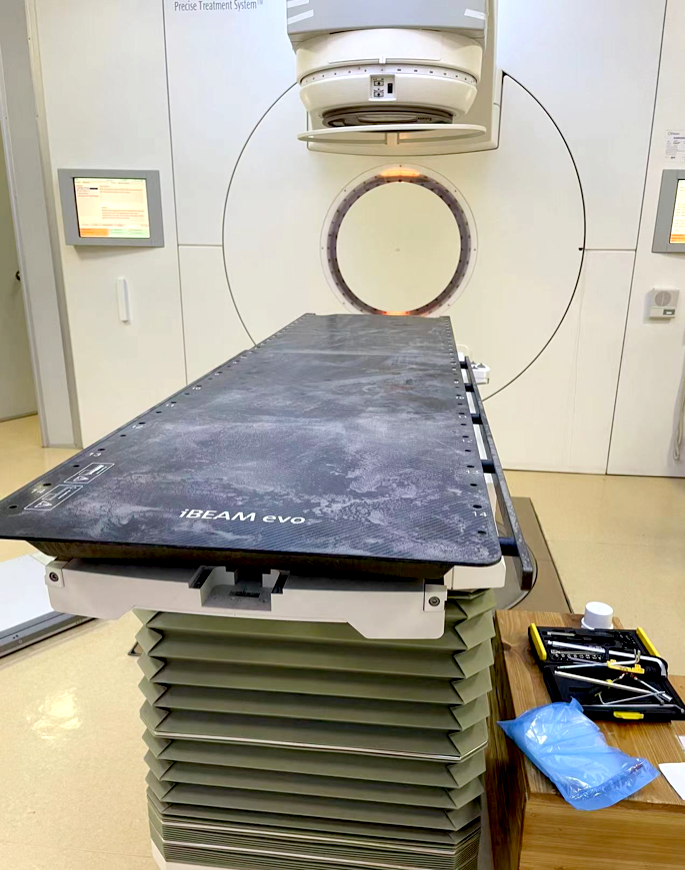
Figure 1: The radiotherapy system and carbon fiber treatment bed being installed in the hospital

Figure 2: The original connector on the opposite side that has not been lost
After communication, the hospital finally decided to cooperate with TPM3D , using 3D scanning, reverse design, and 3d Printer Laser Sintering, using nylon materials to quickly customize this connector, while speeding up the production cycle and reducing production costs, it does not affect the treatment bed. The penetration rate of X-rays ensures the progress of equipment operation.
First of all, because there is no model data, it is necessary to use the other connecting piece on the opposite side to obtain a 3D model through 3D scanning and reverse design. Because the structure of this piece is relatively simple, the scanning and reverse speed are fast, and the data preparation is completed within 2 hours.
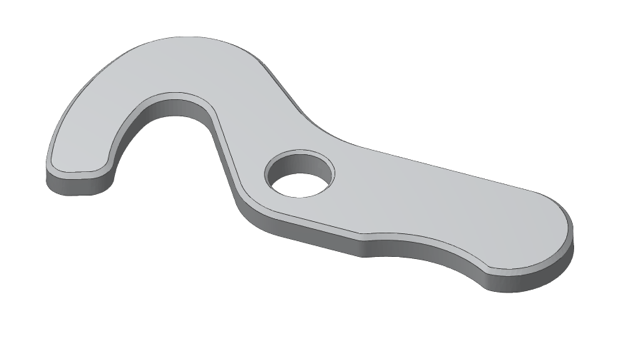
Figure 3: Data after 3D scanning and reverse design
After getting the 3D data of the connected parts, we immediately arranged the printing task. After evaluating the use requirements of this connector, we finally chose Precimid1172Pro BLK nylon 12 material for printing. This is a black nylon polymer material with excellent comprehensive performance. It has good mechanical strength and wear resistance and durability, which can meet this application. The use requirements in the scene, and the material reuse rate is high and the economy is good. The printing model is TPM3D P360, which has high printing speed and high stability, and has both molding size and production efficiency. Cooperating with the one-stop parts powder full-performance processing workstation (PPS), online automatic powder supply can be realized to meet the requirements of continuous production and environmental friendliness.
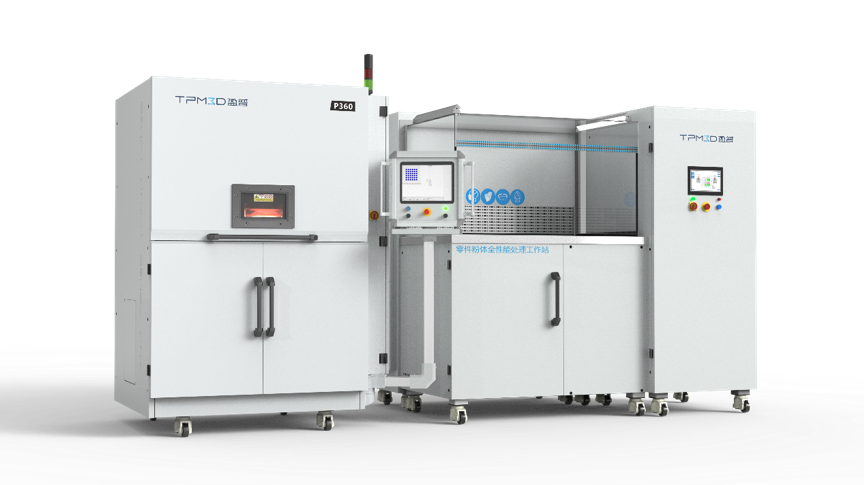
Figure 4: TPM3D P360 Clean Production Solution
After printing, cooling and cleaning powder, we performed a post-treatment of chemical vapor smoothing technology on this joint to make the surface of the part smoother and improve its strength and durability. The chemical vapor smoothing technology uses a special chemical solvent to fumigate the parts in the cabin after vaporization, "smoothing" the surface of the parts, making the surface smooth, dense, waterproof and anti-fouling. In addition, thanks to the reduction of the surface roughness of the part and the disappearance of the crack point, its toughness is significantly improved and it is more durable.
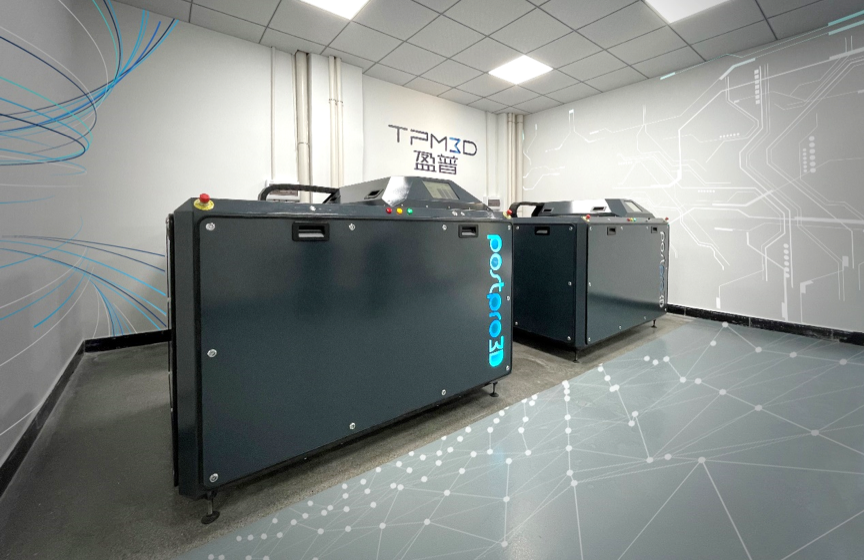
Figure 5: TPM3D is the first to introduce AMT chemical vapor polishing technology in China
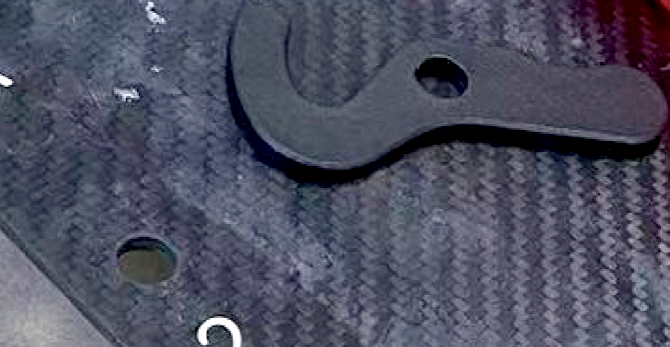
Figure 6: SLS nylon printing connectors being installed
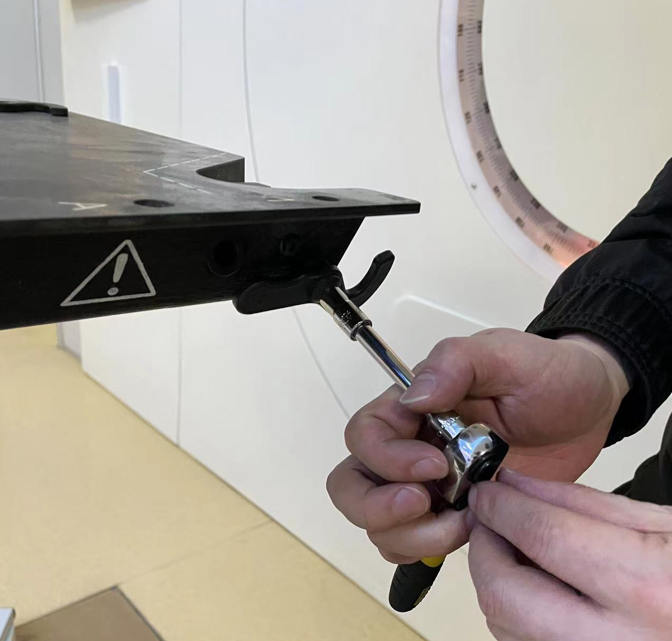
Figure 7: SLS nylon printing connectors being installed
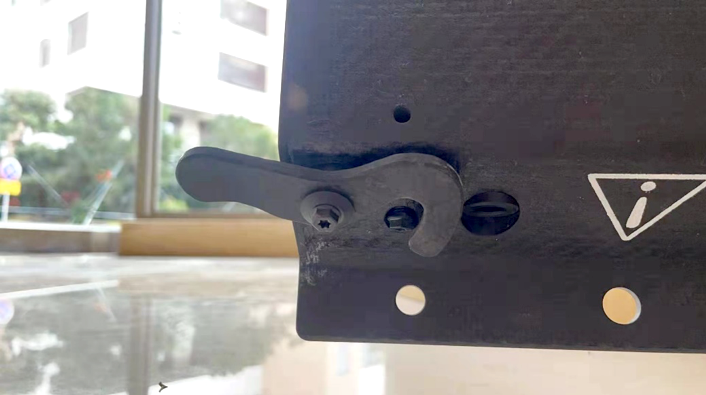
Figure 8: The installed SLS printing connector and expansion board
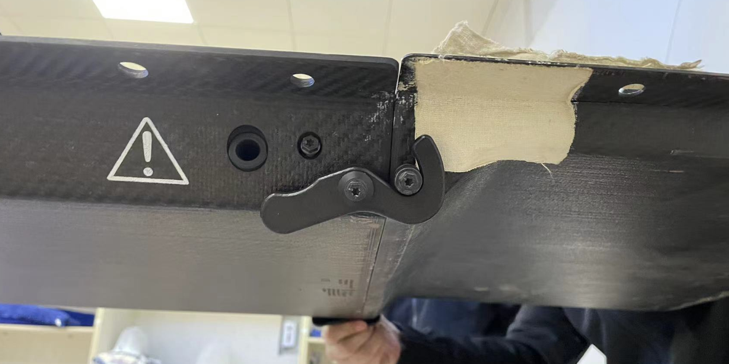
Figure 9: SLS printing connector and expansion board after installation
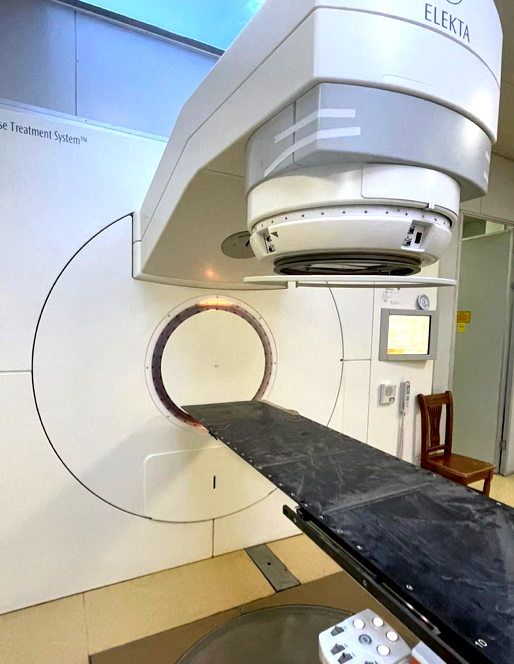
Figure 10: System installation and commissioning completed and ready for use
Considering the small size of the part and the "combined pot" method used in the actual processing process to print and smoke and polish it together with other orders, the actual processing cost is less than 400 yuan. It takes 1 day, which saves the hospital money cost and a lot of time cost, enables the installation and commissioning work to be carried out as soon as possible, and guarantees the time node when the radiotherapy equipment is planned to be put into use. It has once again been verified that SLS laser sintering technology is very suitable for the production and manufacture of small batches of customized final parts, and has the ability of rapid response and flexible manufacturing.
The main component of the radiotherapy system is the medical electron linear accelerator, which is a large-scale medical device that uses microwave electric fields to accelerate electrons to generate high-energy rays, and is used for long-distance external radiation therapy activities in human medical practice. It is widely used in various The treatment of various tumors, especially the treatment of deep tumors. Medical electron linear accelerators can produce X-radiation and/or electron radiation beams. High-energy X-rays have the characteristics of high penetration, low skin dose, and high ray uniformity, and are suitable for treating deep tumors. Electron beams have certain range characteristics and low penetration ability, and are used to treat superficial tumors. The medical treatment bed is the carrier of the patient's radiotherapy. During the radiotherapy process, the impact of the bed board on the absorption of radiation dose should be considered. Therefore, the current high-end treatment bed board no longer uses aluminum alloy materials, so as to improve the bed board's transmittance to X-rays and reduce attenuation.
Application
Recently, when a hospital installed the Elekta radiotherapy system, it was found that one of the pair of connecting parts of the carbon fiber treatment bed iBeam evo expansion board was lost during transportation. The original connector is processed by carbon fiber CNC milling process. The cost of processing this part with the same material is expected to exceed 2,000 yuan, and the processing cycle is longer due to the epidemic. Without this connector, the bed support cannot be achieved. The function of the head, the progress of equipment commissioning and putting into use are expected to be delayed for more than 2 months. On the other hand, although the aluminum alloy CNC processing cycle is short and the cost is low, it will affect the X-ray transmittance of the treatment bed, and then affect the use of the whole set of equipment.
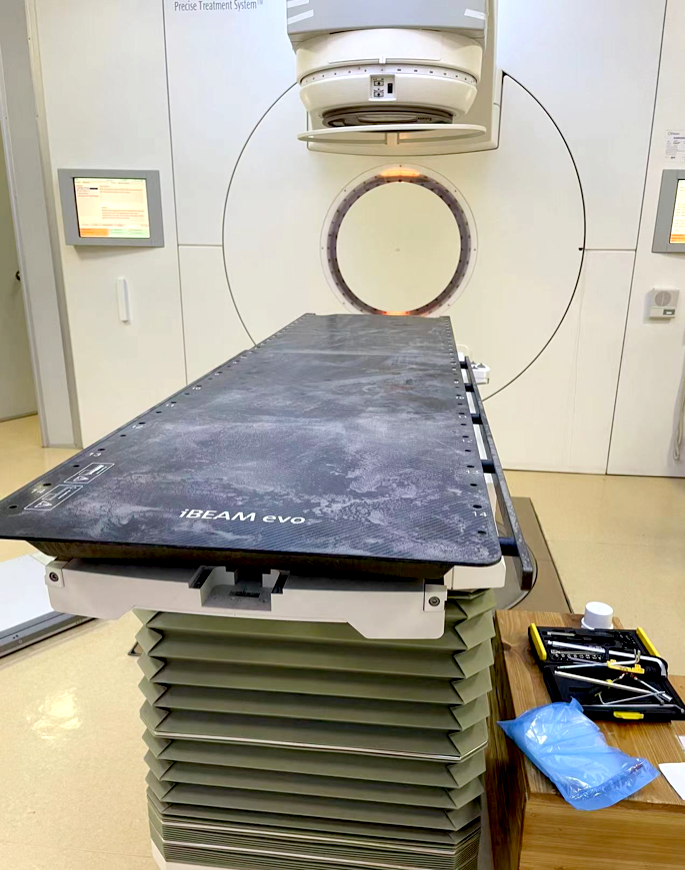
Figure 1: The radiotherapy system and carbon fiber treatment bed being installed in the hospital

Figure 2: The original connector on the opposite side that has not been lost
After communication, the hospital finally decided to cooperate with TPM3D , using 3D scanning, reverse design, and 3d Printer Laser Sintering, using nylon materials to quickly customize this connector, while speeding up the production cycle and reducing production costs, it does not affect the treatment bed. The penetration rate of X-rays ensures the progress of equipment operation.
First of all, because there is no model data, it is necessary to use the other connecting piece on the opposite side to obtain a 3D model through 3D scanning and reverse design. Because the structure of this piece is relatively simple, the scanning and reverse speed are fast, and the data preparation is completed within 2 hours.
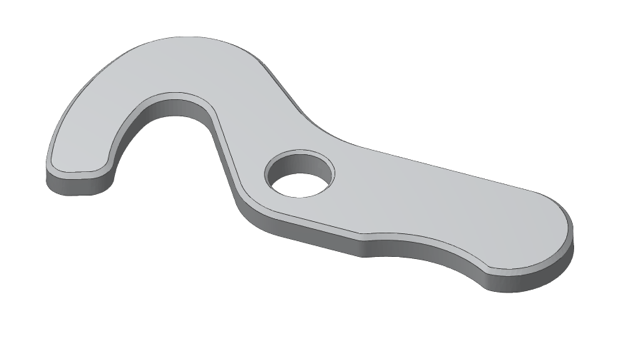
Figure 3: Data after 3D scanning and reverse design
After getting the 3D data of the connected parts, we immediately arranged the printing task. After evaluating the use requirements of this connector, we finally chose Precimid1172Pro BLK nylon 12 material for printing. This is a black nylon polymer material with excellent comprehensive performance. It has good mechanical strength and wear resistance and durability, which can meet this application. The use requirements in the scene, and the material reuse rate is high and the economy is good. The printing model is TPM3D P360, which has high printing speed and high stability, and has both molding size and production efficiency. Cooperating with the one-stop parts powder full-performance processing workstation (PPS), online automatic powder supply can be realized to meet the requirements of continuous production and environmental friendliness.
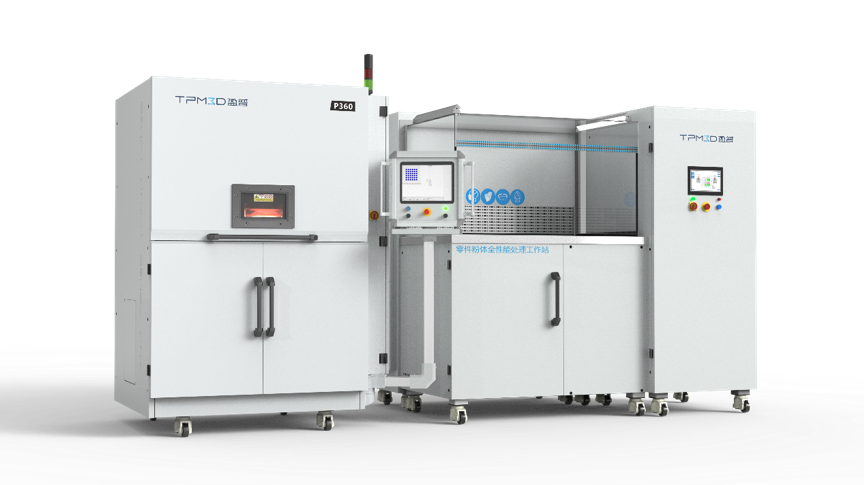
Figure 4: TPM3D P360 Clean Production Solution
After printing, cooling and cleaning powder, we performed a post-treatment of chemical vapor smoothing technology on this joint to make the surface of the part smoother and improve its strength and durability. The chemical vapor smoothing technology uses a special chemical solvent to fumigate the parts in the cabin after vaporization, "smoothing" the surface of the parts, making the surface smooth, dense, waterproof and anti-fouling. In addition, thanks to the reduction of the surface roughness of the part and the disappearance of the crack point, its toughness is significantly improved and it is more durable.
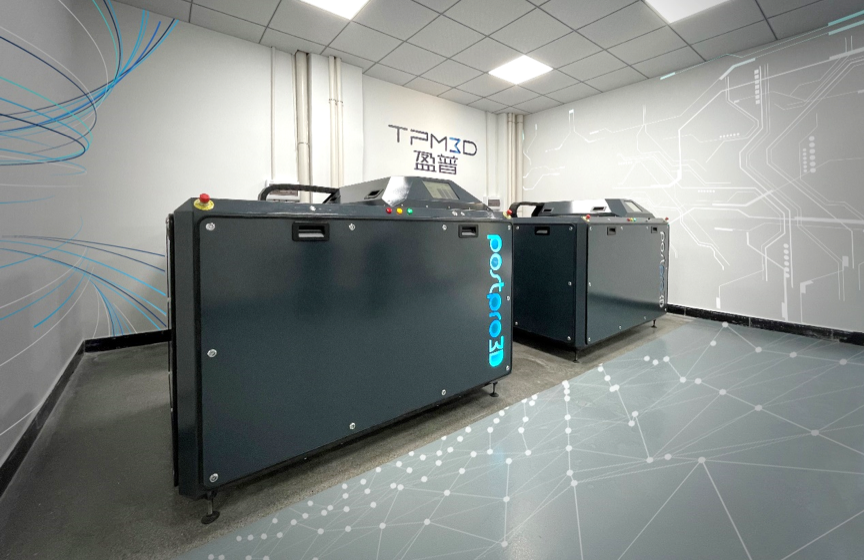
Figure 5: TPM3D is the first to introduce AMT chemical vapor polishing technology in China
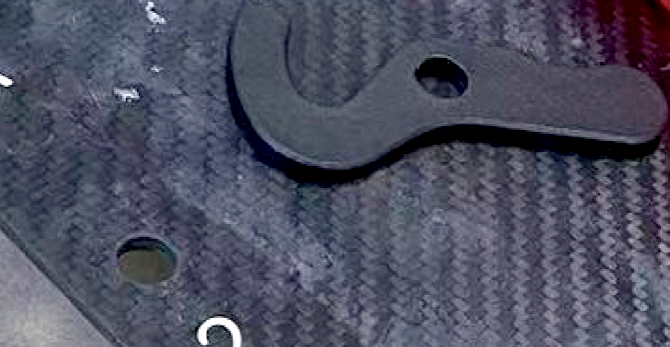
Figure 6: SLS nylon printing connectors being installed
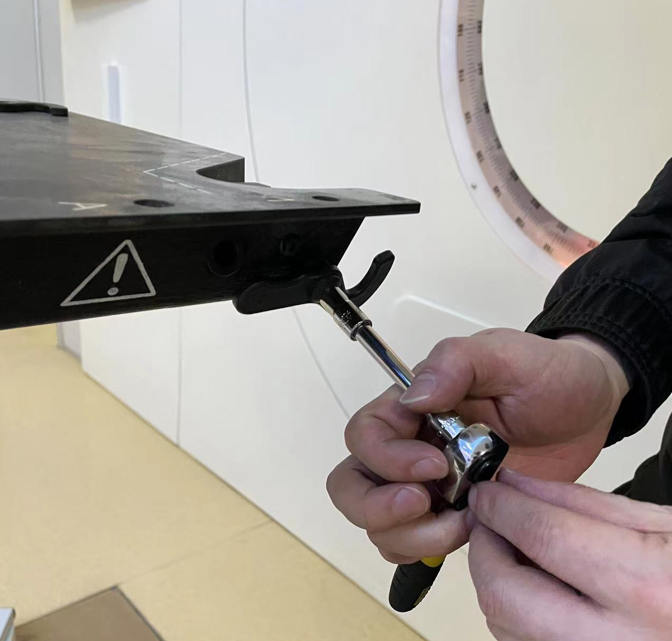
Figure 7: SLS nylon printing connectors being installed
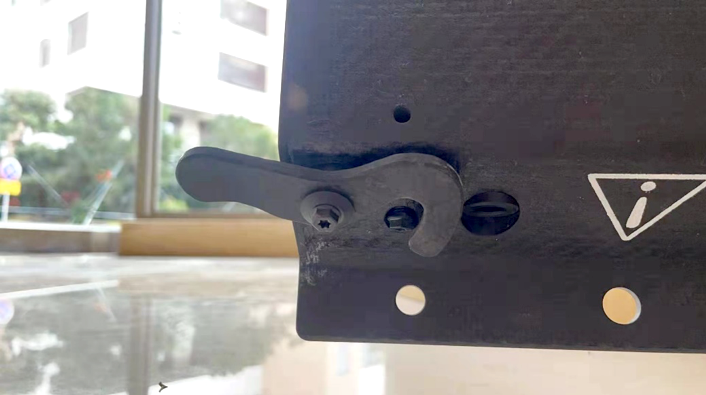
Figure 8: The installed SLS printing connector and expansion board
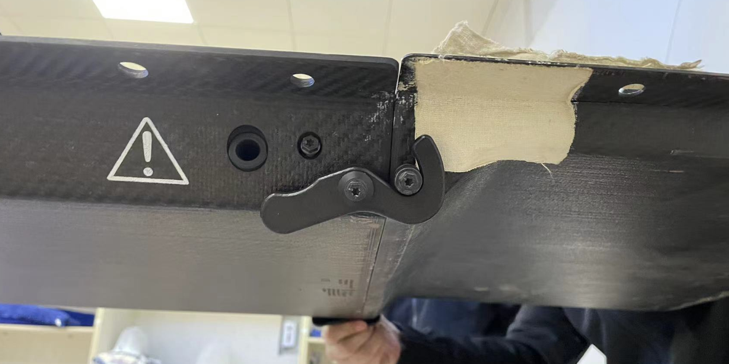
Figure 9: SLS printing connector and expansion board after installation
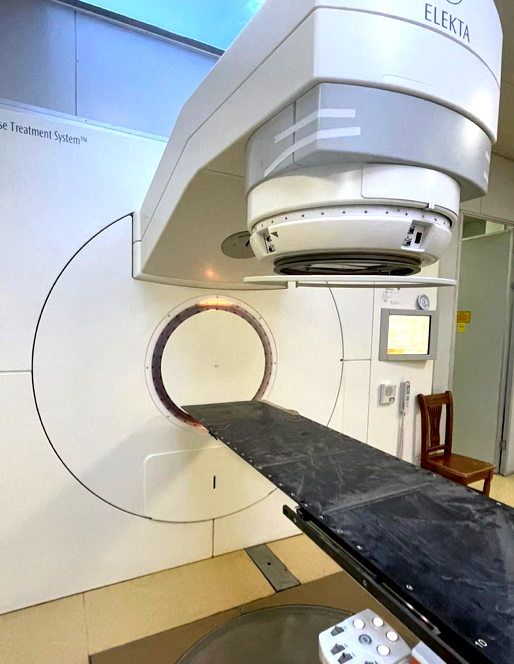
Figure 10: System installation and commissioning completed and ready for use
Considering the small size of the part and the "combined pot" method used in the actual processing process to print and smoke and polish it together with other orders, the actual processing cost is less than 400 yuan. It takes 1 day, which saves the hospital money cost and a lot of time cost, enables the installation and commissioning work to be carried out as soon as possible, and guarantees the time node when the radiotherapy equipment is planned to be put into use. It has once again been verified that SLS laser sintering technology is very suitable for the production and manufacture of small batches of customized final parts, and has the ability of rapid response and flexible manufacturing.